The development of liquid crystal paper is distinguished by the fact that it began at a very strategic stage of the search and preparation of raw materials, which are the basis of the final quality of the product. The heart of liquid crystal paper is the liquid crystals of the same name, complex organic molecules known for their liquid but ordered nature, capable of changing into different phases at different temperatures. Achieving a liquid crystal phase, such as the nematic phase, where the molecules are parallel but not fixed in a lattice structure, is critical because this phase allows manipulation of light transmission, which is essential for display functionality.
To begin this process, manufacturers must ensure not only the purity of the liquid crystal compounds but also the constancy of their chemical composition. Advanced purification methods, such as recrystallization or chromatography, are used to separate the liquid crystals from any impurities that may impair the functional properties of the product. After purification, compounds are carefully tested to confirm their phase behavior and stability, ensuring a reliable transition to useful phases during device operation.
After careful study of the liquid crystals themselves, attention turns to the preparation of the substrates that form the structure to which these liquid crystals adhere. The substrate must be carefully balanced—thin and flexible enough to give the final product the desired paper feel, while maintaining enough strength to protect the encased crystals. Polyethylene terephthalate (PET), a type of polyester, is often the preferred substrate due to its clear, strong, and flexible characteristics. This thermoplastic polymer is made from ethylene glycol and terephthalic acid, and after synthesis is stretched into thin films that will later serve as the canvas for the liquid crystal layer.
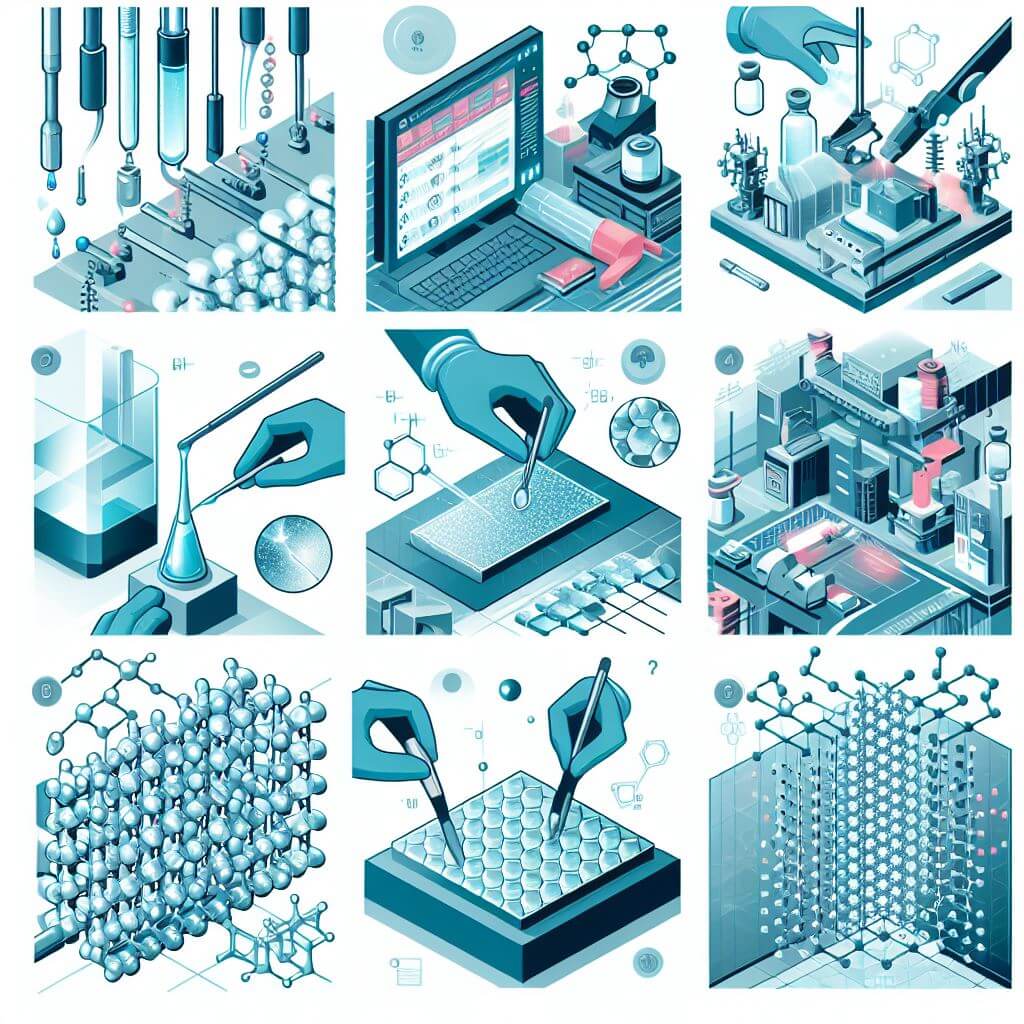
Before applying the liquid crystal compounds, these polyethylene polyethylene films must be surface-treated to improve adhesion and promote proper alignment of the liquid crystals. The surface is covered with a polyimide or similar layer, a key element that will affect the orientation and behavior of the liquid crystal molecules during their deposition. After coating, the substrate with the new leveling layer goes through a curing process, which usually involves controlled exposure to heat or UV light, a step that establishes and stabilizes the chemical functionality of the film.
Deposition and Alignment of Liquid Crystals
The deposition and precise alignment of the liquid crystals onto the substrate represent a pivotal chapter in the manufacturing story of liquid crystal paper. It is here where the magic of this innovative product truly takes shape, as the liquid crystals are meticulously laid down in a uniformly thin layer across the treated surface of the substrate. This stage is particularly critical, as it will ultimately determine the clarity and quality of the visual display.
Manufacturers utilize high-precision deposition techniques such as spin coating or slit coating to achieve this uniform distribution. Spin coating leverages centrifugal force by spinning the substrate at high speeds, causing the liquid crystals to spread evenly across the surface due to the outward force. Slit coating involves a blade or slot die that precisely meters out the liquid crystal material, laying it down in a controlled manner onto the moving substrate.
Once the layer of liquid crystal compound has been applied, the intricate process of alignment takes center stage. The molecular arrangement of liquid crystals is not left to chance; instead, it is carefully directed by the previously applied alignment layer. Surface treatments such as rubbing – where a velvet cloth or roller is dragged over the alignment layer – create micro-grooves that guide the liquid crystals to lie parallel in a single direction. This establishes the pretilt angle, which is fundamental for uniform optical characteristics in the liquid crystal layer.
Alternatively, photoalignment techniques can be employed where light patterns are projected onto the treated surface, inducing molecular alignment without the need for physical contact. This method offers advantages in reducing the potential for contamination or physical damage to the delicate surface while still achieving the requisite orientation of the liquid crystal molecules.
During this time, environmental conditions are closely controlled to maintain an optimal atmosphere for the liquid crystals to align and settle. Temperature, humidity, and airborne particulates are managed within precise tolerances, as any deviation can induce defects in the liquid crystal layer. Such defects can hamper the functionality of the liquid crystal paper, resulting in poor image quality or inconsistencies in display.
Assembly And Sealing
Once the delicate task of depositing and aligning the liquid crystals has been carefully accomplished, manufacturers move on to the assembly phase, a process that requires precision and engineering precision to ensure the integrity of the final liquid crystal paper form. In this step, the two substrates—each with surfaces filled with liquid crystals—must be joined together, creating a well-sealed environment to protect and hold the liquid crystals in place.
The substrates are carefully placed together to leave a uniform gap between them, often only a few micrometers. A key component to creating this gap is the use of spacers—tiny balls or fibers that sit between the pads and maintain the required distance. These spacers must be evenly spaced to prevent image distortion that can occur if the spacing is inconsistent.
Once the substrates with their liquid crystal content and spacers are perfectly aligned, sealing becomes the next critical task. The perimeter of the substrate sandwich is coated with a special adhesive or sealant that is supposed to prevent contaminants such as moisture and dust that can disrupt the performance of the liquid crystals. The sealer was chosen for its ability to bond substrates securely, as well as provide a flexible seal that can withstand the physical stresses associated with using liquid crystal paper. It must also be inert in the presence of liquid crystals to prevent any reaction that might affect its properties.
The sealing process uses precision equipment to apply the sealant in a clean and controlled manner, ensuring the absence of voids and air bubbles that can impair its barrier properties. In addition to physical barriers, the sealant plays a conservation role by maintaining the stability of a precisely calibrated internal atmosphere, protecting the liquid crystal material from oxidation and degradation over time.
At this stage of assembly, quality control is critical. Manufacturers should check the seal for integrity and the overall construction for any signs of displacement or ingress of impurities that could cause product failure. This often involves both visual inspections and testing in specific environmental conditions to simulate the problems the product will encounter during regular use.